第1回 金属材料 疲労破壊の基礎
本日より、技術士の福﨑先生による機械設計者向けの金属材料に関する連載を全4回でお届けいたします。
第一回は「疲労破壊の基礎」です。
はじめに
疲労、摩擦摩耗、腐食の3つは金属材料の不具合として広く一般的な現象である。
そして金属の疲労破壊は多くの機械部品にとって避けて通れない問題である。
疲労破壊は小さなねじやシャフトだけでなく、自動車、鉄道、建物、橋などの大型構造物でも起こるため、人命にかかわる問題である。
そのため、疲労破壊のメカニズムを理解し、その対策をとることは非常に重要である。
1 疲労破壊のメカニズム
1-1 疲労破壊のメカニズム
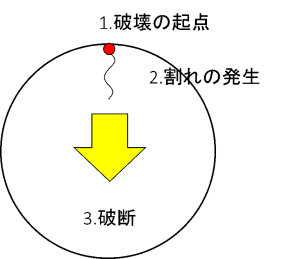
図1 疲労破壊の模式図
疲労破壊はまるである日突然金属が破壊するように見えるが、実際には小さな割れが少しずつ進行して最終的に破壊が起こる現象である。疲労破壊のメカニズムでは主に3つの段階を考える。1つ目は起点、2つ目は割れの進行、3つ目は最終的な破断である。この様子を図1に示す。
起点は不純物介在物や応力集中などによる材料中の弱い場所となる。割れの進行は応力負荷によって起点から発生した小さな割れが徐々に進行する過程である。そして割れが進行すると材料の断面積が減少するので、材料に負荷される応力は大きくなる。そして、材料の限界を超えると一気に最終的な破壊が起こる。このような過程によって疲労破壊が起こる。
疲労破壊はその過程よりいくつかの特徴がある。1つ目は疲労破壊は材料に応力が繰り返し負荷されることによって破壊する現象である。1回や数回の応力負荷で破壊する現象ではないのである。
2つ目は比較的小さい応力でも起こることである。通常、材料が変形したり破壊するためには降伏応力や引張応力以上の応力を負荷する必要がある。しかし、疲労破壊では降伏応力よりも小さい応力でも繰り返し負荷されることで破壊が起こる。
3つ目は最終破壊まで大きな変形が少ないことである。これが疲労破壊が突然破壊したように見える原因でもある。疲労破壊は途中の主な過程は小さな割れの進行なので、材料に曲げや変形など目に見える変化は少ない。
金属材料が疲労破壊を起こすことは古くから知られており、その対策や取り組みもたくさんあるが、本稿では大きく2つの側面について注目する。1つ目は材料の高強度化であり、2つ目は応力集中の緩和である。
材料の高強度化とは材料自体を疲労破壊が起きにくいように強く強化することである。これは鍛造、熱処理など金属材料的な取り組みである。
応力集中の緩和とは材料の形状や負荷される応力を減少させて出来る限り破壊の起点を減らす取り組みである。これには材料力学や破壊力学などが必要になる。
疲労破壊の起点は表面の応力集中が注目されやすいが、全ての疲労破壊が表面起点から起こるとは限らない、材料内部の不純物介在物や欠陥などの弱い場所を起点にして疲労破壊が起こることも観察されている。どちらの場合でも材料にある弱い場所が疲労破壊の起点となる。
疲労破壊に及ぼす影響はとても多い。それは疲労破壊に強くなることもあれば弱くなることもある。おおよその方向として材料を硬く強く強化することは疲労破壊に強くなるので良い影響となる。一方応力集中や不純物介在物など材料の弱点となることは疲労破壊を起こしやすくなるので悪い影響となる。
1-2 疲労試験
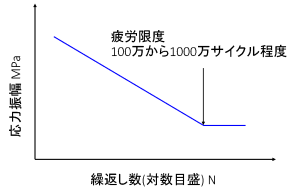
図2 疲労試験のS-N曲線
引張試験や硬さ試験のような多くの材料強度試験と同様に疲労破壊についても強度試験がある。ただし、疲労破壊の応力負荷は種類が多いので、その応力負荷に合わせた疲労試験を選択することが重要になる。例えば曲げ応力が重要な製品については曲げの疲労試験を行うのがよい。しかし、もし引張圧縮の疲労試験を行った場合、曲げ応力と引張圧縮応力は異なるので、その製品にとって適切な疲労試験データとならない。
疲労試験の種類はたくさんあるが、疲労試験の評価としてはS-N曲線で行われることが多い。S-N曲線の例を図2に示す。これは応力振幅と破壊に至るまでの繰返し数をグラフに表したものである。高い応力振幅では短い回数で破壊する。一方、応力振幅を低くすると繰返し回数が長くなる。
そして多くの鋼では一定値以下の応力振幅になると、どれだけ応力振幅を繰返しても疲労破壊を起こさないことが起こる。この応力を疲労限度と呼び、設計上重要な値となる。疲労限度はおおよそ100万から1000万回の応力振幅頃に表れることが多い。
絶対に疲労破壊を起こしてはいけない製品は疲労限度以下の応力となるように設計しなければならない。ただし、全ての材料に疲労限度があるわけではない。アルミニウム合金などでは1000万回を超えても疲労破壊が起こるため、明確な疲労限度が表れない。
2 疲労破壊の事例
疲労破壊は最近の問題ではなく、船、建物、飛行機など大型構造物を金属で生産し始めた時から起きていることである。これらの事例は失敗事例や事故事例として取り上げられる。その中でも歴史的、技術的に大きな事例がいくつかある。それを表1に示す。この中でもジェット機コメットの墜落は疲労破壊の事例としてよく取り上げられるので、本稿でも取り上げる。
表1 金属材料破損に関係する大きな事故例
年代 |
名称 |
主な原因 |
1912 |
タイタニック号沈没 |
鉄の低温脆性など |
1940 |
タコマナローズ橋崩壊 |
自励振動、橋の構造など |
1942 |
リバティ船沈没 |
鉄の低温脆性、溶接欠陥、応力集中など |
1954 |
ジェット機コメットの墜落 |
応力集中、試験方法、フェイルセーフなど |
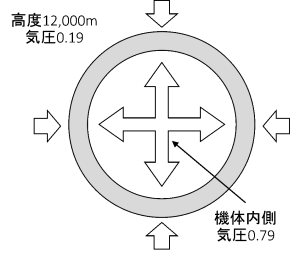
図3 飛行機の機体に負荷される応力
ジェット機コメット墜落については多くの資料や記事があるので詳細はそちらを参考にされたい。ジェット機コメットは1953~1954年の間に3回墜落していた。その時のフライトはおよそ1000回程度であった。ただし1機は不明である。
飛行機は上空高く飛行するので、地面とは気圧が異なりおよそ0.2気圧程度になる。しかし飛行機の内側は人がいるので外側よりも圧力は高めにしている。そのため、飛行機はフライトの度に機体内側から外側に向けて応力が負荷されている。フライト時に機体に負荷される応力の模式図を図3に示す。
もちろん当時も機体に負荷される応力は把握しており、耐久試験も行われていた。それなのに予想よりも早いフライト回数で疲労破壊を起こしたのである。原因として耐久試験と耐圧試験を同じ機体で行っていたことが指摘されている。なぜなら、たとえ耐久試験で疲労破壊の元となる小さな割れが発生してもその後に圧縮試験を行うと、その小さな割れがふさがってしまい疲労の進行が止まってしまうからである。
そのため、実際のフライトとは異なる応力状況で試験したため、適切なデータが取れなかったのである。他にも疲労破壊が起きた窓が直角のため応力集中を起こしやすい形状だった。
この事故の反省として耐久試験と耐圧試験は別の機体で行うことや窓やドアは直角にしないで角に丸みをつけて応力集中を起こしにくくする工夫が取られている。
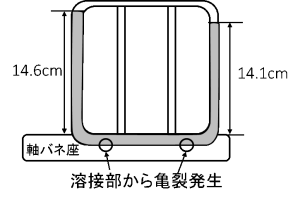
図4 新幹線の台車の亀裂の様子
また、比較的新しい事例として2017年の新幹線の台車亀裂事故がある。博多発東京行の新幹線で走行中に異音や異臭を感じ名古屋で点検した時に割れを発見した事例である。この事例は国土交通省に重大インシデントとして報告されている。
この時に新幹線の台車と呼ばれる部品に割れが発生した。直接の原因としては台車と軸ばね座と呼ばれる部品を溶接する時に寸法精度が悪く修正するために板厚を削りすぎてしまい強度低下して割れが発生したのである。台車の割れの様子を図4に示す。
これら大きな事例だけではなく、疲労破壊は様々な機械部品で起こる可能性のある問題である。特にボルト、ギア、ベアリングなどの部品はほとんどの機械に使われているが、これら部品は常に応力をうけているので疲労破壊が起こりやすい。
3 応力の種類
応力と似た言葉に荷重がある。荷重とは力そのものであり、単位はN(ニュートン)やKgfである。応力とは荷重を断面積で割ったものであり、単位はPa(パスカル)となる。
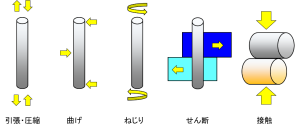
図5 応力の種類
材料の負荷される応力はその向きや位置などから大きく5種類に分けられる。これを図5に示す。1引張圧縮、2曲げ、3ねじり、4せん断、5接触である。このような応力の違いは疲労試験の種類にも反映されている。疲労試験でも引張圧縮疲労試験、回転曲げ疲労試験など応力の種類によって分けられている。
そしてそれぞれの応力の計算式も異なっている。詳細は割愛するが、例えば引張圧縮応力では単純に荷重を断面積で割り負荷応力を計算するが、曲げや応力は曲げモーメントや断面係数を元に計算する。断面形状が円形、角材でも計算式が異なるのである。
材料と応力の関係を評価する時に基本的な試験として引張試験がある。引張試験とは材料に引張応力を負荷してその時の変形挙動を評価する試験である。引張試験の例を図6に示す。
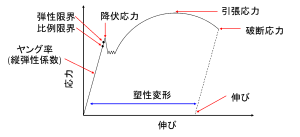
図6 引張試験
材料に引張応力を負荷すると最初は直線的に応力とひずみが上昇する。この時材料に負荷した応力を取り除くと元の形状に戻る性質がある。これを弾性変形と呼ぶ。そしてこの時の応力とひずみの関係からヤング率(縦弾性係数)が求められる。
弾性変形を起こしている材料にさらに応力を負荷すると、降伏応力が表れる。降伏応力を超えると材料は塑性変形を起こす。塑性変形とは応力を取り除いても元の形状に戻らない状態である。そして降伏応力を超えると応力は少し低下する。
降伏応力を過ぎるとしばらく一定の応力となるが、再び応力が上昇するようになる。そして最大応力となる点が引張応力と呼ばれる。引張応力を超えると応力は低下して最終的に材料は破断して引張試験は終了する。
引張試験は強度的に重要な応力やひずみが測定されるが、特に降伏応力と引張応力は重要である。降伏応力を超えると材料は塑性変形を起こし、引張応力を超えると材料は破断するからである。
また、アルミニウム合金のように明確な降伏応力が表れない材料もある。その場合は0.2%ひずみの時の応力を0.2%耐力と呼び、降伏応力と同様の扱いを行う。
引張試験片は棒や板など様々な形状が規格されているが、いずれも中心部が凹んだ形状である。降伏応力を超えて塑性変形する時は主に中心の凹んだ場所が伸びるように変形する。そして引張応力を超えると中心部の一部がさらに凹み最終的にはそこから破断する。
4 応力集中

図7 応力集中
材料に応力を負荷した時に均一、一様な材料はどの場所も一定の応力が負荷される。しかし、材料の中に割れなどの亀裂があると材料の中の応力分布が変化する。応力は亀裂を貫通できないので、亀裂を回り込むように力が働く。そうすると亀裂先端には応力が集中するようになる。これが応力集中である。応力集中の模式図を図7に示す。応力集中は形状の影響を受けやすく、亀裂先端が細くなるほど応力集中は強くなる。反対に亀裂先端がまるくゆるやかになれば応力集中は低下する。
応力集中は亀裂など不具合だけの問題ではない。機械部品や構造物には直角の角、溶接の端など断面積や形状が異なることはよくある。これらはできるだけ応力集中しないように角部や端部に適度な丸みやRをつけることが好ましい。
5 亀裂のある材料の評価
亀裂のない材料と亀裂のある材料では当然き裂のある材料の方が弱い。そして、どの程度の亀裂によって材料の強度が低下するのか、など亀裂のある材料の評価は破壊力学などで議論される。
亀裂のある材料の評価として応力拡大係数と破壊靭性がある。応力拡大係数とは亀裂付近の応力状態を表し、破壊靭性とは亀裂が進行する最小の応力を表す。亀裂先端はとても鋭く応力集中を起こしているが、亀裂を進行するためには一定の応力が必要になる。それが破壊靭性である。破壊靭性が高い材料は亀裂が進行しにくく、破壊靭性が低い材料は亀裂が進行しやすい。
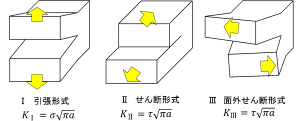
図8 亀裂の負荷モード
また亀裂に負荷される応力の向きによって応力拡大係数は主に3つの形式に分けられる。1引張形式、2せん断形式、3面外せん断形式である。材料に負荷される応力は5種類だったが、亀裂については3種類となる。亀裂の負荷モードとそれぞれの応力拡大係数を図8に示す。
また、破壊靭性は材料の厚さが細いほど高く、厚くなるほど低下する傾向がある。これは破壊する時に亀裂の進行が平面応力から平面ひずみというモードに変化するためである。
破壊靭性は3点曲げ試験やコンパクト試験によって測定することができる。これはASTMなどでも規格されている。材料の形状、亀裂の長さ、負荷荷重から計算される。
福﨑技術士事務所 福﨑 昌宏 2005年 千葉工業大学大学院 工学研究科 金属工学専攻を修了。 同年 金属加工メーカー、2013年に建設機械メーカー 研究開発部に入社。2017年に技術士(金属部門)取得。2019年4月より独立開業。 金属材料の破損・不具合に関する分析調査を専門とし、これまでに歯車など機械部品の材料開発や品質改善、疲労破壊の破面分析などについてコンサルを手掛ける。同時に若手の技術者向けの金属材料に関する講演や執筆を多数行う。 |
![]() |