リードタイム 第2回 リードタイムの短縮【開発】
目次
リードタイムの短縮【開発】
前回はリードタイムについてお伝えしましたが、今回はリードタイムの短縮【開発】についてです。
開発リードタイムは、設計・試作~試験・設計変更を、仕様を満足するまで繰り返すことから、長期化することが多い工程です。
仕様通りの性能が出なければ、何度も設計~試験をやり直すことになり、納期を延期しなければならなくなることもあります。
無理のあるリードタイムを設定したために、検討事項の確認や製品の性能が不十分なままで納品した後に不良が発覚すると、
追加で余計なコストがかかり信用も失ってしまいます。
そこで、開発リードタイムを短縮するためには、どうすれば良いかを考えなければなりません。
1.開発環境の見直し
開発する製品の種類や規模によって、工程の作業内容は変わってきます。
開発リードタイムの短縮するためには、まずは開発システムを見直すことが効果的です。
昔から使っている作業手順や規定なので問題ないかもしれませんが、現代では合わないようなこと、手順や規定を増やしすぎて逆に無駄になっていることもあるかもしれません。
新しいものの導入は出来なくても、社内の開発環境を見直して、無駄や遅延の原因を取り除くだけでも、十分リードタイムを短縮できます。
しかし、効率を良くするためには、システムや新しい考え方やなどを導入することで、更に良くできます。
2.開発に使用するシステムのデジタル化
データの共有システムや3D-CADと構造解析などのシステムを活用して開発環境をデジタル化することで、開発業務を効率化し、手戻りの発生を防ぐことで開発リードタイムの短縮に繋がります。
開発データは毎日更新されるものです。
色々なデータや文書のような、業務に必要な情報をファイル(紙)で保存していると、誰かが資料を持って行って直ぐに確認できない、最新の情報を持っていないために古いデータで作業を進めてしまいやり直しになる、といったトラブルが発生しかねません。
データで共有していれば、このようなトラブルが避けられて、結果としてリードタイムの短縮になります。
3.開発システムの共通化
開発チームで使うシステムの共通化により無駄な時間をなくすことが、リードタイムの短縮に効果的です。
3D-CADの場合ですが、複数のCADソフトを使っていると、チーム内でもデータのやり取りをするためにSTEPやIGSなどの中間データに変換しないと開くことができません。
変換によって形状が崩れてしまうことや、作った形状が消えるなど、データに異常が発生することがあります。
また、履歴が消えてしまうことが多いので、後からの修正が難しくなります。
表計算ソフトでも、分割したセルがおかしくなることや、数式が数値になってしまうことがあります。
そういったソフト間のやり取りで発生する齟齬を、その都度確認や作り直していては無駄な時間が発生し、リードタイムが長期化する原因となります。
4.共通部品を使い、情報を共有する
製作部品や市販部品の情報を共有することで、部品の検証に使う時間が短縮できます。
何の部品をどんな条件で使ったのかの実績があれば、新しい製品開発のたびに新規で部品を設計・製造するために、仕様の確認や製造方法を考える必要がなくなります。
複数の製品で同じ部品を使用するのなら、大量に製造・購入して在庫にすることで、調達の手間を減らすことができます。
また、生産ラインでは何度も同じ部品を使うことになるので、作業をシンプルにできると、取り扱いを間違えるといったトラブルの防止にも効果があります。
こういった情報を共有化することで、開発工程の効率化だけではなく、他部門の工程も効率化でき、トータルリードタイムを短縮できます。
5.3D-CADの活用によるロスの削減
機械設計で使用する3D-CADの機能を活用して、設計~作図にかかる作業時間の短縮や試作(製作)してからの設計不良やミスが原因の手戻りを削減できます。
例として、干渉チェックができる機能あります。
部品の形状とねじ類を全て組み込んだアセンブリデータについて干渉チェック機能を使うことで、干渉している個所がわかります。
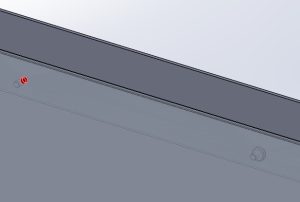
※上記画像では、穴が空いていないので、ねじと干渉しています。
設計が複雑になればなるほど、確認の時間と細かいミスを見逃す機会が多くなりますが、PCのスペック次第で数分で確認ができます。
検図で気が付けば良いのですが、気づかずに進んでしまうと製造からの手戻りになり、大幅なリードタイムのロスになります。
6.シミュレーションの活用によるプロセスの削減
専門知識が必要になりますが、3D-CADのデータを活用して、各種シミュレーションにかけることで、様々な計算や試験・実験にかかる時間が削減できます。
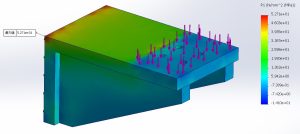
※強度シュミレーション
シミュレーションの結果だけで判断するのは危険ですが、正しい知識と経験のもと使うことができれば、確認の為に試験をするだけで良くなり、戻りのプロセスを大幅に削減 できるので、それだけリードタイムも短縮できます。
設計~設計変更までのプロセスは、設計から試作を製作して、試験・実験の結果をフィードバックして設計変更を何回もするわけですから、とても時間がかかります。