鉄鋼材料の熱処理と表面処理の基本 第2回 鉄鋼材料の表面処理
技術士の奥野先生に「鉄鋼材料の熱処理と表面処理の基本」について全3回で連載いただきます。第2回は、鉄鋼材料の表面処理についてです。
鉄鋼材料の表面処理は、「熱処理によって素材の表面を改質し、疲労特性を改善すること」ということができ、その手法によって熱処理、加工硬化、表面被覆に分けることができる。
いずれの手法も、製品の表面に亀裂が入らないように、また、亀裂が入っても、その亀裂が大きくならないようにすることを目的としている。
めっき処理も表面処理に分類されるが、めっきは主に耐食性を上げる手段であることから、本稿では割愛する。
目次
1.硬化熱処理:物理的表面硬化法
(1)高周波焼入れ
硬化熱処理は、物理的に表面を硬化する方法であり、高周波の電流を素材に通し、抵抗加熱することで焼き入れを行う方法である。電流の周波数を変えることによって加熱深さを変えることができ、予熱が要らず短時間で行えること、圧縮方向の残留応力が発生するため、普通に焼き入れを行うよりも硬くできる、などのメリットがある。
高周波焼き入れは、比較的低炭素の素材の表層の効果、部分焼き入れに用いられ、通常の焼き入れに比べて加熱・冷却を迅速に行うことができるが、短時間の処理のため、炭素の拡散が十分に行えず、焼き割れ・焼きむらなどが生じやすい、という欠点がある。炭素の拡散が材料特性上問題になる場合は、高周波焼き入れの前に焼き入れ焼き戻しを行う、焼入れを行う部位の形状や寸法などを考慮に入れる、などの対応を行う必要があることも多い。
また、高周波焼き入れをおこなった材料を後工程で研削加工する場合は、研削割れを防止するために、温度が150℃以下になるように研削の条件・方法を検討する必要がある。
(2)レーザー焼入れ
レーザー焼き入れは、高周波焼異例よりも小さい、薄い領域に焼きを入れることができるため、熱影響部をさらに小さくでき、早く冷やせるため高い硬度を得ることができる。また、部分的に熱を加えると発生しやすくなる熱歪みについても、高周波焼き入れと比べると軽減される。欠点および対策方法については、高周波焼き入れと同じと考えて良い。
2.硬化熱処理:化学的表面硬化法
(1)浸炭
浸炭は、炭素を材料の表面に入れてやることで、表面をより高炭素とし、それを焼き入れることによって硬さを得る方法である。高炭素鋼は、硬くて加工が難しいことが多いため、加工の段階では低炭素で加工性を確保しておき、成形後に表面に炭素を導入し強度を上げる考え方で用いられる。
浸炭には、固体浸炭、液体浸炭、ガス浸炭の3種類の方法がある(表1)が、いずれの方法であっても、鋼に炭素を供給する役割は一酸化炭素(CO)が担っている。
① 固体浸炭
浸炭材として、浸炭促進剤(炭酸バリウムや炭酸ストロンチウム)を混ぜた木炭を使い、製品を埋め、加熱する方法で、浸炭後は緩冷却後、あらためて加熱して焼き入れを行う。
② 液体浸炭
浸炭材にシアン化ナトリウムの塩浴を使う。これを酸化させてシアン酸ナトリウムとし、加熱することで発生する一酸化炭素で浸炭を行う。
液体浸炭ではシアン酸ナトリウムから一酸化炭素を発生させる段階で、原子状窒素も発生するため、窒化も同時に行うことも可能である(→(3)項の「軟窒化」を参照)。浸炭だけを行う場合は、700℃以上(800〜950℃程度が多い)に加熱する。
③ ガス浸炭
浸炭材として炭化水素ガスを用い、これに空気を混ぜて高温にすることで熱分解反応を起こさせた変成ガスの雰囲気で行う。熱分解反応によって、浸炭性を持つ一酸化炭素だけでなく、脱炭性を示す酸素や二酸化炭素、水素などを発生するため、事前に変成ガスの雰囲気を確認すること、および、目標となる表面硬さ・硬化層深さから、変成ガスの雰囲気を調節することが必要である。
実操業においては、脱炭性を示すガスの濃度を測定するセンサーを設置し、導入する炭化水素ガスや空気の量を調節する。
(2)窒化
窒化は、浸炭と比べて、鉄に固溶する量が大きいために浸炭よりも容易に導入できること、また、炭素の場合と異なり、オーステナイト変態やマルテンサイト変態など、寸法変化を伴う組織変化を起こさない点で優れているが、処理時間が長く、窒化層の厚みがばらつきやすい、という欠点もある。
窒化は、ガスまたは液体(塩浴)によって行う(表2)。ガスを用いた窒化法では、窒素源としてはアンモニアガスが使われ、処理時間を短くするために、二段窒化や酸窒化などの方法が開発されている。
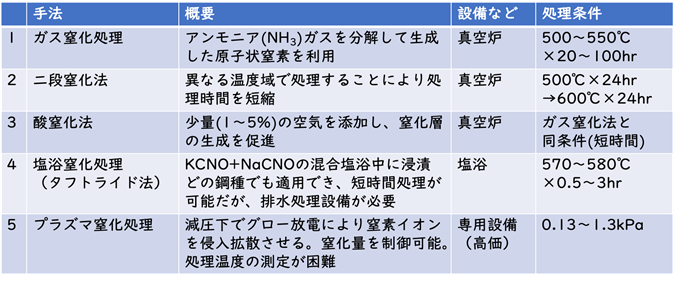
【表2】浸炭処理の種類と特徴
液体で行う窒化は、液体浸炭で用いられた方法と同様の塩浴を用い、一酸化炭素が発生しない低い温度域で処理を行う。
プラズマ窒化処理は、ガスを用いて、高電圧による放電を使って原子状窒素を作り出す方法であり、雰囲気温度を測定するのが難しい反面、窒化量を制御可能であり、窒化量のばらつきを抑える処理方法である。また、この方法ではアンモニアを使わずに窒化を行うことができるため、環境負荷が少ない方法でもある。
(3)軟窒化
軟窒化とは、窒化と浸炭を同時に行う処理を指し、表面に化合物の層を作ることを主目的とし、窒化とほぼ同じ方法で、窒化に比べて短時間で処理を行える。原則として拡散による浸透を必要としないため、材料を選ばず特性の改善が可能、という特徴を持つ。
内部に原子を拡散するためには、軟窒化処理の後、熱処理を行う。これにより、窒化物の拡散層が生成される。
窒化及び軟窒化に共通して、これらの表面処理を適用する場合、特に、耐久性が要求される工具鋼や金型鋼の場合は、設計段階で以下の4つのポイントに留意する。
①耐久性を重視する場合は事前に調質処理を行う
②変形を防止するため、処理温度は調質の焼きもどし温度よりも低くする
③皮膜の剥離を防止するため、硬さ分布の勾配をできるだけ緩やかにする
④処理前に製品表面の肌荒れをできるだけ少なくする
3.加工硬化:ショットピーニング
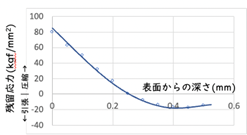
【図1】ショットピーニング材の
残留応力分布例
(材質SUP6, 0.7mmカットワイヤショット)
ショットピーニングは、物理的に表面状態を変える方法であり、表面に塑性変形を与え、圧縮残留応力を与えることで、強化する方法である。ショットには、1mm以下のワイヤーを切断したものや溶鋼粒などが用いられ、製品の強化深さによって決められる。
ショットピーニングを制御するパラメータはショットの投射速度および投射時間であり、適切な処理を行うことで、疲労強度が向上する。この疲労強度は、圧縮残留応力によって生じる(図1)。ショットの投射速度が小さいと処理効果が得られない反面、逆に大きすぎるとオーバーピーニングを生じ、表面に亀裂や断熱変形帯(図2点線の直上、断熱剪断帯とも呼ぶ)が生じ、逆に疲労強度が低下する。
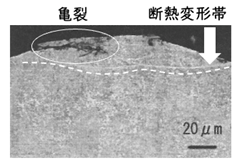
【図2】オーバーピーニングの例
亀裂と断熱変形帯が認められる
ショットピーニングは物理的な変形を加え、鉄の結晶構造に転位を導入する処理とも言える。この転位は外力によって容易に移動するため、経時的に残留応力が消失し、強化した効果が薄れていく。これを防止するため、転位部に炭素や窒素原子を移動させることで転位を動きにくくする(転位固着、コットレル雰囲気形成ともいう)ことを目的に、ショットピーニング処理の後200℃程度で低温焼きなましを加える処理が用いられる。
4.表面被覆:CVDおよびPVD
表面処理技術として用いられる方法のうち、熱処理、浸炭窒化、およびショットピーニングは、材料そのものを改質する技術であるが、PVDやCVDは、材料の基本的な性質は変えずに、材料表面に新しい素材を追加して強化する技術である。
CVD(化学気相成長)は、製品の表面で原料を化学反応させる技術であり、PVD(物理気相成長)は原料を蒸発させて製品表面を被覆する技術であり、当初はそれぞれの技術で適用可能物質が限定されていたが、現在ではいずれの方法でも対応可能な物質が増えている。
(1)CVD:化学気相成長
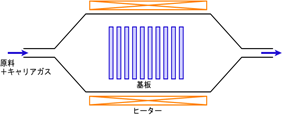
【図3】横型熱CVD装置の構成図
CVDは、製品の表面で原料を化学反応させ、表面を被覆する技術であり、皮膜を厚くでき、皮膜と製品の密着性も高くできる。反面、被覆膜には引張応力が働くため、外力による膜の破損(チッピングや欠損など)が比較的生じやすい、という欠点があり、この欠点を克服すべく、成膜をより低い温度で行うMT-CVD、引張応力を軽減するための技術開発が進められている。
基本となる熱CVD法は比較的簡便な設備構造で、ガス組成と温度を制御することが容易である(図3)。また、触媒を付与して反応性を向上させるために触媒を付与したり、原料に有機金属材料を用いる方法などの応用技術もあり、広く用いられている。
(2)PVD(物理気相成長)

【図4】IP法の原理
PVDは、原料を蒸発させて製品表面を被覆する技術であり、CVDと比較して低温で成膜ること、密着性はCVDに劣るが、被覆膜には圧縮応力がかかっており、CVDに比べると強度(硬度)が高くなる特徴がある。
基本的なPVDとしてイオンプレーティング(IP)法があり、真空蒸着に加え、蒸発粒子をイオン化して帯電させ、基材に衝突させることで、皮膜の製品への密着性を高める方法である。イオン化させる方法として、アーク放電を用いる場合はアークイオンプレーティング(AIP)と呼ばれる。
PVDは比較的薄い膜を生成することもあり、蒸発粒子が製品に均一に当たっていない場合はドロップレットと呼ばれる欠陥を生じやすい。これらを抑制するための技術開発も数多く行われている。
奥野技術士事務所 代表 大学院修士課程(金属工学専攻)修了後、大手鉄鋼メーカーに入社。主に鉄鋼製造の現場において操業技術管理、設備管理、品質管理を担当し、その後、製品企画、プロセス技術開発、技術企画、品質保証業務(QMS品質管理責任者)を経験。2021年に退社し技術士事務所を設立、金属製品製造における品質管理、および航空宇宙製品の品質保証について、現場目線での再発防止の仕組みづくりを積極的に推進している。 現在、公財)新産業創造研究機構の航空ビジネス・プロジェクトアドバイザー、産業技術短期大学非常勤講師を務める。 |
![]() |